By Olivia Trusdale
“When life gives you lemons, make lemonade.”
This popular phrase is one of those “easier said than done” things. It isn’t always easy to sweeten what’s been soured, especially in the midst of the unprecedented times we’re living.
During the chaos and seeming madness, we can easily lose sight of the beauty in our everyday situations. (And sometimes, it can be really hard to find or see that beauty!) So how do we stay positive and insightful when we’re living through a literal PLAGUE PANDEMIC?!?!? And societal tensions? And a volatile economy? And don’t forget those murder hornets!
As TEAM PERKA, we are trying our utmost to “Keep It Simple and Stress-free” (K.I.S.S) So in this article, we’re going to be sharing 5 of our favorite tips for positive, hopeful, and connected OPTIMISMS.
Tip 1: Post positive sticky notes around your work and living spaces. It’s almost impossible not to smile when you’re looking at a cheerful note, from you, for you, to you! According to a Time Magazine article, posting constant visual reminders of positive thoughts or even inspiring photos can significantly improve your mood, your outlook and increase your confidence.
Some fun ideas for these happy little notes are “Smile!”, “It’s going to be a good day!”, and “You can do it!” You might also want to utilize your favorite quotes and Bible verses. There are endless possibilities. Focus on reviewing these positive messages frequently. Anything that sends you happy thoughts and “good vibes” does affect the psyche. (And if your happy sticky notes are spread throughout one of Perka’s hybrid buildings, that provides an extra burst of positivity and good MOJO!
You can virtually have a quantum vortex of optimism from a quality building, affordably constructed, comfortably furnished, AND boosted by happy thoughts posted all about the premises. How does it get better?
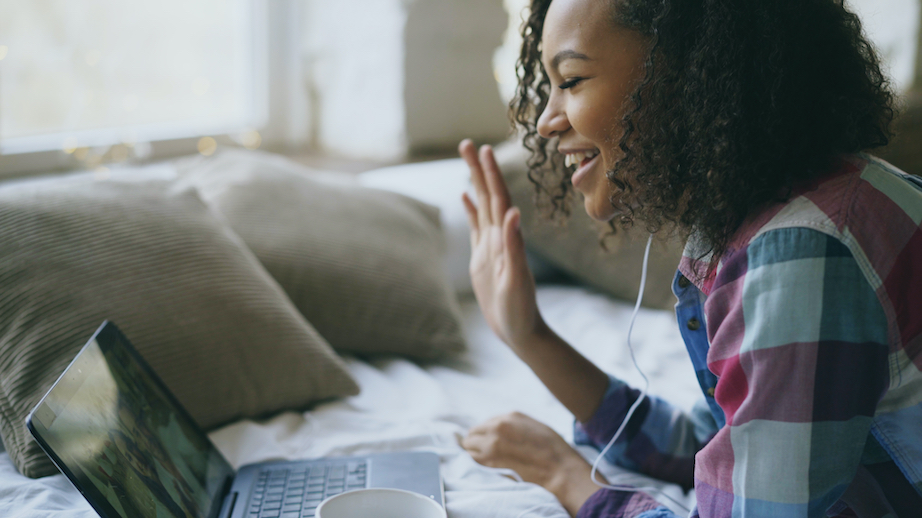
Tip 2: Stay connected with friends and family. Countless studies have proven that spending time with friends increases your happiness. Even though you may not be able to physically gather with the people you love, there are many other platforms that make it possible for you to stay connected. Skype, Zoom, Microsoft Teams, and Google Meet are popular and fast evolving online choices.
And there is always the old fashion phone call, postcard, letter or even a telegram! Yes telegrams are still possible – but maybe more so as a novelty! And of course there is a new digital app attempting to replicate the Telegram “feel” as an online chat messenger!!
Whichever way you choose, it’s important to keep communications open with the people you care about, and with anyone you basically have a meaningful relationship with. Just having that assurance of knowing that you aren’t alone helps you feel better about yourself and your situation.
Also being informed in a timely fashion of any “important or change in circumstances” can totally remove uncertainty that leads to “stress”! — The truth is, we’re all going through challenges of various degrees, right now, in real time.
We as TEAM PERKA are also living through this very same volatile yet expanding world like you. A GINORNOUS component of our culture – most of which pertains to creating more joy and less stress — is all about COMMUNICATING!! WE have a “hashtag” acronym we use every chance we get — #DWC. No, it’s not Dancing with Canadians or Drinking with Cowboys… it’s DON’T WAIT COMMUNICATE!!! We would love to be a part of the stress-free solution “lemonade” making that life is presenting to you. Contact us and let us know how we can be of service!
Tip 3: Let others know that you care about them and what they’re going through. While this piece of advice is not necessarily an obvious idea to foster positivity, reaching out to others can make a big impact on your own happiness, not to mention theirs.
When you help others, something happens in our brains and heart that promotes a realization of how blessed you are, inspiring gratitude and furthering more caring generosity. Plus, investing in other people (whether it’s with your time, talents, money, words, etc.) can be extremely gratifying. And you will just feel better, knowing that you’ve made a difference in someone’s day and life. Not only does it make you feel more positive, but they grow in positivity, too, because they received kindness from you. It creates a ripple effect. Which, if paid forward, can literally become perpetual in kinetic potential! Try it. If it’s not working just yet… increase the dose. This ideal is an important element in our Team’s culture as well!
Tip 4: While it’s good to reach out to others and connect with friends and family, don’t forget to take some time for yourself, too. Taking a break and having some fun- at the appropriate times- can help you refresh, relax, recharge, reignite, refocus and thus work (or play) more efficiently, especially when it’s time to begin again on your necessary tasks.
You shouldn’t ignore your problems, but brief distractions can help you return to them with new ideas and a fresh perspective.
Team Perka seeks to be a trusted advisor to help you look at your situation from as many perspectives as possible. From over 200 years of combined experience from the advisor team alone – you can benefit from the wisdom that life offers from making mistakes… and while there is a lot of training and education built in to our team – there is little to replace someone who has been through many relatable situations and has “seen a thing or two”!!
Tip 5: Stay flexible! BE flexible… this is one of those things that is less skill and almost all ATTITUDE!!! It’s a CHOICE!!! Being loose, calm, open, go-with-the-flow-, NO PANIC can really make a difference when seeking out STRESS FREE SOLUTIONS!
What is happening or is going to happen, is often just going to happen. The main thing you have control over is the way you respond to it. You can treat everything as a “problematic” challenge of extreme proportions or consequences OR you can see it as a new opportunity/way to serve and grow.
Worry less about “if you make a mistake”, or can’t respond “on some particular time line” per se; but yes do the best you can, with the resources you have and COMMUNICATE!! #DWC. Keep all concerned parties up to date and aware of the roadblocks, challenges or obstacles that need to be overcome!
Some things just are or are not in total synch with our moment to moment needs. Stay calm, poised and open to any, all and even “other” solutions! You will always receive the gift of knowing or understanding more about how to or not to possibly do or say something. Own it. Apologize if it serves. Make amends, reparations and KEEP MOVING. Keep evolving. It’s a secret to Happiness!
With TEAM PERKA, seeking to be calm, poised, reflective and specifically flexible is one of the five core values in our “S.A.F.E.R.” solution manifest. Flexibility means adapting in the midst of difficult, changing, unexpected, unplanned, or challenging circumstances and being open when change comes to work WITH IT. To seek out and then deploy a solution… Own it. But still grow with it.
Though this may sound presumptuous, we do sincerely hope that buying a new building is a change or opportunity that does comes your way. And when that presents itself, whether it came from a lemon or not – you can be assured that our Team will be here, able and willing, to help you stay positively on track, connected to purpose, calmly caring for your situation and for YOU personally – so that we can be poised to flexibly arrive at the best, most serving, joy filled solution.
For more information about our “Safe, Affordable, FLEXIBLE, Easy, Resilient” buildings, customer service, and company culture as a whole, contact us here.